Expert Panel: Predicting the Future of IT in Supply Chain Management
Join expert guests Pete Schroeter, Tod Grams, and Dave Poggi as they discuss the future of information technology in supply chain management in this informal manufacturer's panel. These industry veterans delve into trends in manufacturing today, transformative technologies, and the future of data management as it relates to supply chain management.
Questions
- What are some of the key innovation trends you are seeing in manufacturing today?
- What technologies have been and will be relevant to help drive these innovations?
- Given the recent economic challenges, in what ways are manufacturers pivoting?
- What technologies have been the most impactful in aiding the pivot and future success?
- Are your biggest challenges process related or technology related? Why? What are some of those challenges?
- Do you see collaboration (or lack thereof) as a business challenge? What about collaboration with shop floor staff?
- What technologies do you see emerging that are making the lives of rank and file manufacturing workers easier and allow for more tightly integrated collaboration?
- Large software vendors are investing heavily in AI. In Microsoft's case, we see a lot of AI Capabilities coming to Microsoft Azure. Do you see AI taking a larger role in the future of IT in manufacturing? Why?
- Data and access to data is changing the way we make business decisions. Has access to Data made a large impact on your manufacturing operations? How?
- From a Business Continuity Perspective, do you feel like most manufacturers are prepared to weather future disasters? Does new and emerging technology like Azure Site Recovery and Azure Backup change this in your opinion? Have we learned our lesson from COVID?
- Do you feel like the industry 4.0 movement is leading the charge in terms of modernizing technology for Manufacturers? Why?
- Are cloud technologies like those in the Microsoft Azure and M365 platforms helping to achieve the goals and practices laid out by the Industry 4.0 movement?
Meet the Panelists
Pete Schroeter
Principal - Schroeter & Associates
Pete Schroeter is Principal and sole member of Schroeter & Associates, an independent manufacturing and supply chain consulting practice started in 2002. He is a 35+ year veteran in the food, chemical, pharmaceutical, and packaging industries, supporting companies by improving their cost, inventory, and service performance.
Tod Grams
Business Development - Disher
Tod Grams, Business Developer for IoT, Digital Tech Solutions and Electronics development is a skilled leader with a demonstrated history of working in Electronics, IoT, IIoT, Automation and Digital Tech Solutions. Skilled in hardware and software development for digital tech solutions, Tod has been with Disher for the last 6 years, prior to which he spent 21 years as a developer.
Dave Poggi
CEO & Principal Consultant - Software InsITe LLC
Dave Poggi is the CEO and co-founder of Software InsITe, a technology strategy, consulting, and development company focused on manufacturing and distribution. Dave improves his clients’ business processes and builds applications and integrations that improve margins. Technically inclined, Dave’s skills focus on Microsoft's stack, including Dynamics Business Central, Azure, A.I., SQL, .NET development, PowerApps, Power Automate, and Power BI.
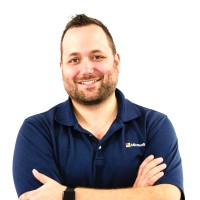
Panel Host/Technology Expert - InsITe Business Solutions
A regular content contributor for InsITe Business Solutions, Andy Syrewicze has experience managing IT solutions for a diverse array of enterprise clients. He provides CIO-Level Strategic planning and operations services, as well as helping enterprise clients align Cloud and Office 365 services with business needs. With almost 2 decades of IT experience, Andy is heavily involved in the wider IT community in a number of different ways, including, podcasts, webinars, blogging and public speaking.
1.What are some of the key innovation trends you are seeing in manufacturing today?
Pete: Manufacturing is a big, massive area, so I think it's helpful to break it into a couple of pieces: Process Manufacturing and Discrete Manufacturing.
A good way to look at the differentiation between the two is that in Process industries, you make things in batches and put them in packages. A process product could be a bottle of ibuprofen, 100 count, where you make a bunch of tablets and you put hundred counts in bottles. Or it could be chemical surfactant and you put it in a 195,000 pound railcar.
On the Discrete side, you make things in niches. You know you're going to make 1000 seatbelts today.
And so the manufacturing strategy, how you setup and configure varies between the two. Some of the innovation that we're having the discussion on can vary between the two as well. So in process industries, there's manufacturing strategy issues. What do you do with high volume items versus low value items? How do you set up your floor? How do you go after things like quick changeovers?
And that is a product of two things. One is physical things: How do I make it go from configuration A to configuration B? But how do I get the information to bear to know whether I should make that change over - or not? What's demand tracking at? What's the order stream look like? What's the shipping stream look like etc etc?
On the discrete side, you have different strategies, such as cellular manufacturing, modularized, manufacturing. Maybe you can figure that you're in a “product family”, and then moving from one item in that family to another item in that family minimizes your your wait time, your queue time to get from here to there.
So a lot of innovation, both on the physical side as well as information, coming to bear to make those sorts of sorts of changes. I like to say “Geez, if we can understand how to make decisions with real time data, that cuts a lot of poor metrics down to size.” Often inventory and improvements in service improvements.
So innovation is a confluence of physical setup and configuration and information to bear, and I think we've got some questions on information later in the dialogue and I'll talk about transaction data versus master data as we get to that point.
Andy: Sounds good. Tod, Dave, any thoughts?
Tod: Pete brings up a great point and that's relative to the trends that you're seeing with data. I know we'll get into data a little bit later, but those innovation trends really start with the company and in the “why” you know.
But ultimately with the data, you're making decisions, and that real time data is so critical. Having that critical data that's available being processed in real time (as opposed to going back and having to take a look at the data) that criticality, that timing piece is a huge trend in manufacturing that is really, bar none, the most critical step in manufacturing today.
2. What technologies have been and will be relevant to help drive these innovations?
Dave: It starts with connectivity; we've got a tremendous amount of information that our machines on the floor are generating. But we have to have that connectivity to say “How do we get that data?” To Pete’s point and what Todd mentioned, if we don't have that data, we can't make decisions on it. It’s full-time connection to the equipment on the floor to the operators so that as data is coming in, we're gathering it, we're able to make decisions on it.
Some technologies like artificial intelligence and cognitive services and vision that are things we can bring to the floor now that used to be expensive or difficult, but now have really been commoditized (not in a negative sense). There's definitely product differentiation between the capabilities out there, but in the sense that we can now apply these where we used to not be able to afford to. We can put vision in places that used to be “We'd never go there. That's not our number one machine. We aren't going to do it.” Now, that's the kind of thing we can get past and put real.
This gives us the ability to see what's going on to collect the data that correlate with that and to apply some of the newer capabilities around artificial intelligence. Get real time schedule information, things that used to take the end of the shift or the end of the day. And heck, at one point, the end of the week. Now those things are happening real time.
Andy: That sounds good. Pete or Todd, anything you want to add?
Pete: Well, to Dave’s point, one’s ability to put real time information in place to bear on decisions has real business impact. Real value prop. So if you can put information and make decisions that help you extend a production run or cut off a production run, that certainly has real time customer service revenue impacts in one case. Or maybe working capital inventory impacts/cost impacts as another case.
It's not just “kind of fun and it would be nice if we could do this” ,it has real measurable business impact. Put that real time information, maybe with the use of some AI that the technical guys can bring to the table, in place.
Tod: To add to that point for both what Pete and Dave are saying, those benefits that you are referring to are things like global and regional factories having that data intelligence in real time, no matter where you are in the world. So other things are like supply chain management. You know real time supply chain management oversight. Also, and we talk about it all the time, and that is the predictive maintenance. That's where the AI comes in. You need to keep those machines running, and in order to keep those machines running and keep people constantly building widgets and devices and things like that, that predictive maintenance becomes a critical piece to keep in the factories efficient and flowing.
3. Given the recent economic challenges, in what ways are manufacturers pivoting?
Andy: Pete, I'll let you take a stab.
Pete: Many companies need to precisely map capacity to demand, so I see a significant emphasis, more so than on the demand side, on the capacity planning side. The demand side is pretty important as well, but if you're going to pivot into product line extensions or pivot to a different product or change the way you manufacture or do a contract manufacture - all those strategies require some really good solid precision capacity planning.
Get back to this notion of real time: So where are you in your production runs? What does your mix on the production floor look like? How does that relate to your demand? Can you make those alterations in real time as the clock is ticking? Or are you more discreet and have to wait until the end of the day to make your decision for the next day? Big differences in inefficiencies.
So capacity planning is something I see is really, really challenging manufacturers, and that goes into the extended supply chain as well. So if you are a discrete manufacturer and you got 42 different parts that go into your finished good, then you have to have a real good understanding of the inflow of material of those 42 parts from however many of our suppliers are providing those. The communication game becomes really important. It's not just the supply chain within the four walls of the manufacturer, but outbound to the supplier base or upstream of the supply base.
And for that matter, to capture the demand statement, you need a good understanding of what’s happening downstream in your customer base. So it's not just the the four walls or the planning exercise for capacity, but upstream and downstream become very important. Real time information becomes really important. Collaboration becomes very important. How you wrap process around all this becomes very important. Extended supply chain capacity planning is where I see a lot of emphasis these days.
Andy: I'm starting to see a trend here. Some of the same keywords starting to be thrown around. Interesting to see. So Tod, I'll let you take a stab at it. Are you kind of seeing the same things on your end?
Tod: Yeah, absolutely. Capacity planning certainly is one of the things. And again, we talk about efficiencies. We talked about machines, processes, and things like that. How impactful that is is like the difference between either making a part or not making a part, or making a delivery or not making a delivery. And most manufacturers, I'm assuming, at this point cannot not make right now - They need to make their shipments.
So better tools in the way that the manufacturers can pivot is the key to being agile. And if you could be agile, keep machines running, manage not only incoming flows of equipment and product, but then also the outgoing and understand the supply and demand, the better off we're going to be at being efficient.
4. What technologies have been the most impactful in aiding the pivot and future success?
Andy: I want to swing to the technology part of the discussion and bring it back to Dave. Dave, any thoughts on that end?
Dave: Sure. There's a couple of things that have been super important for folks, one being the ability to connect and get visibility to that floor. You know, look at us here, remote; that's something a number of manufacturers are having to deal with right now. That means they need virtual eyes and ears on the floor. That spells out getting visibility, getting your production, even if it's the basic stuff. What's our cycles? What's down? What logging is occurring?
Most of the manufacturing equipment out there has PLC's and a tremendous amount of data embedded in those machines. Exposing that bringing it out and letting that be visible across the organization. Whether you're in the same building or the same County, or even across the globe, that's hugely valuable.
And there's been an emphasis on those manufacturers who thought everything they did was local. Well, local doesn't mean what it used to with covid. People are starting to recognize they need to have that visibility. Even if we still want to walk the floor, that isn't always going to be practical.
Andy: Todd, Pete, any thoughts on it?
Tod: Dave brought up a great point in the connectivity element. I mean, those tools exist. Cloud Services, the main ones; you know the Amazons, the Googles. Those are the key elements to getting that data to where it needs to be processed and understood. So you need to get it from the localized machines and PLCs, etc too. Those data warehouses, if you will. You can look at the data and make real time decisions with that. So connectivity, bar none, is probably one of the most impactful technologies that we see today.
Pete: To add to that, I think your brief comment on data itself. Key downfalls that I've seen are issues of latency or accuracy or inaccuracy or incompleteness. And if you look at data, I like to slice that one up into a couple of buckets as well.
You've got transaction data and you've got what I would call master data. Transaction data is things like orders, inventory levels, inventory status, production data, etc. Master data might be things like practical capacity in manufacturing or throughput, or bombs, or routings, or packaging Masters. Those kinds of things. If either or any of those are less than stellar, your application and your IT functionality is going to produce an undesirable or an inaccurate result and lead to a poor decision. It's going to have business impact.
So I see an interesting trend: I see a number of companies putting somebody in charge of master data or data management. Somebody either in the technology group or in some cases in the functional manufacturing or supply chain groups because there's a recognition that if we're going to rely on technology to drive these decisions, we better have data that's up to date, not latent, and complete.
Andy: Kinda comes back to the whole concept of “garbage in, garbage out” as far as data goes, right? You gotta make sure it's the current data that you're going to be actioning on, so that's fantastic insight.
5. Are your biggest challenges process related or technology related? Why? What are some of those challenges?
Andy: Well, I just kind of want to switch gears a little bit here. Todd, I think it was you that mentioned a little bit earlier about some of the challenges you’ve been facing in the industry and the kinds centered around process. Are your biggest challenges process-related or technology-related? The last couple years it seemed like the two have become kind of really interwoven. But, you know at least the way I look at it, the process side is kind of like the human element, whereas the technology side is the technology, right? So which one of those is more of an everyday struggle as opposed to the other, and why?
Tod: That's a great question, and here's a canned response for you: we're actually seeing a mix of both, but mostly I would say it's process related. That's primarily because there's many companies that haven't even started their digital journey yet, and there's a rather large leap of faith even just to get started in regards to the investment that is required. These companies are needing to develop their why; Why are they doing this? What data is critical? What's the value of me doing it? And then architecting an IT infrastructure that's companywide. And then finally rightsizing and integrating the right technologies and softwares into their processes. So some of their biggest challenges are more process related just in getting started.
Other companies, however, are much further along their digital journey, and their biggest challenges are the technology related elements because they already had the infrastructure in place. So yes, we do see a mix of both, but in the end you know either way, most of the IT architectures and cloud services and technologies - they all exist today, it's just applying them. Engineering companies and solution providers like InsITe and Disher are great at being able to help integrate those technologies into their processes. The key certainly is getting started. But I would say that process related is more of the challenges that we see today.
Andy: Gotcha, that's kind of expected from my own experience in the manufacturing space. Pete, Dave, have you seen the same, or something different?
Pete: Yeah, the only thing I'll add to Tod's commentary there is that I think there's an organization and skill level element to that as well. I don't think the marketplace is generating the quantity of combined process and technology-skilled people to move in the direction that we're talking about. I have heard from virtually every one of my clients we have a talent acquisition issue and usually it's a comment that's related to skill levels. And I'll just leave that there because that could be a whole other conversation, but I think there's an organization skill level element attached to this topic.
Dave: I agree there's a gap in terms of the engineering expertise and the process technology combination. We're seeing folks look at things like IoT and saying “Wait a minute. I need to bring that in in order to leverage that to turn around this problem where I don't have enough people who know how to run these machines”. You know the days where we used to rely on Joe to be able to set up the machine on Mondays, and hopefully we could run it all week. You know, terribly expensive lacks efficiency and is a huge risk. Now we're seeing people use HMI and other things so that they can have operators repeat preferred setups for equipment and be able to get things right. That drives a lot of efficiency when we start to have repeatable setups and quicker changeovers. And those things make a massive difference to the productivity of manufacturing.
6. Do you see collaboration (or lack thereof) as a business challenge? What about collaboration with shop floor staff?
Andy: Good insight guys. I want to build on that a little bit and I'm going to circle back to you, Tod, on this one. I want to talk about collaboration a little bit. Collaboration, at least to me, kind of ties in with process, right? On the process side, do you see a lot of struggles with collaboration as a business challenge? And more specifically, what about collaboration between front office and shop floor?
Tod: That's a very good question. Collaboration, and the tools used for collaboration, is more important than ever in today's day and age, and we already talked a little bit about it. I believe agility is the keyword that comes to mind here when you're looking at market volatility, pricing pressures, Covid supply chain shortages, and even labor. We just talked about it, labor changes. They’re all examples of pain points that can be addressed through collaboration technology integration that’s focused on fast and efficient collaboration or monitoring or even text messaging. So the strong collaboration element with manufacturing staff on the floor is certainly all the more critical and all the more reason to have machines that utilize great HMI or UI/UX technology to allow for that human-centered design that can really make the human/machine interface much more user friendly and collaborative. Dave hit on that earlier and I totally agree that more user friendly that an HMI is or utilizing a UI/UX interface, the more efficient that those individuals are going to be. Collaboration, especially from front office to the shop floor and being able to have that real time data to pivot when needed is absolutely critical. But if you don't know how to pivot, or it's not user friendly, then there's going to be some downtime associated with that.
Andy: Dave, Pete: any any thoughts?
Pete: So building on that, I do a lot of sales and operations planning, which tries to map a demand statement of some sort, some definition, to set up a supply response. And so a lot of times you hear comments like “the manufacturer guys can't respond or they can't do this or they can't do that”. Well they’re oftentimes not set up for success by the commercial side who has to be tasked with bringing a demand statement in proper granularity and planning horizon to the table. Because a lot of the tradeoffs that the manufacturing side are trying to make are near term/long-term, lot size, and resource assignments-oriented. If there's not a structure in place to do that sort of repetitive cycle for collaboration, starting with the commercial side and then translating that in approximately reasonable time to the floor to respond and say yes, I can do this or no, I can't do that we could do this instead. If you don't have that in place, the collaboration falls short. And again it has business impact, usually on the service or cost side.
7. What technologies do you see emerging that are making the lives of rank and file manufacturing workers easier and allow for more tightly integrated collaboration?
Andy: So I'm thinking things like Microsoft 365, or some of the IoT technologies in Microsoft Azure and things like that. What are your thoughts on that, Dave?
Dave: We're seeing clients have great success with Microsoft Teams. We're doing things like setting up Teams that are oriented towards a given manufacturing cell or production line and then bringing things that used to run around on emails or text into a central channel where everybody can act. We've got the ability now to bring messaging into that, so when we see things happening out of those machine centers, we can post them right into that channel. We're combining the intelligence of the equipment and the connectivity we have with people's ability to be agile and shift and react and make sure everybody is on the same page in terms of A- what are the priorities, and B- what's actually happening right now and what we want to do to adjust to it. That kind of collaboration technology, it's not hard. It's amazingly enabling and starts to bring people together around the data, which is really more important than just having the data.
Tod: To add to that, Dave, you're absolutely right and hit the nail on the head. One of the technologies that you're seeing that’s off the Microsoft platform is Power BI, Power Automate, and Power Apps. Those are exactly what Dave is referring to, and having that key data and collaboration and information available on the spot/peer to peer/immediate, if you will, and those tools like Power BI, Power Automate, and Power Apps really help that collaboration.
Pete: And the only thing I'll add to that is again, back on the skill set topic of a moment ago: When you put those sorts of technologies in place, don't skip on the training budget, right?
Andy: (chuckles) Right! It's funny because that's one of the areas that you so commonly see people skip out on. It’s like, “Hey, we've installed this great technology. It's no good if nobody can use it right”?
Pete: Absolutely, absolutely.
8. Large software vendors are investing heavily in AI. In Microsoft’s case, we see a lot of AI capabilities coming to Microsoft Azure. Do you see AI taking a larger role in the future of IT in manufacturing? Why?
Andy: We're talking about data and access to data and how it changes the manufacturing decision making process. One thing that I wanted to touch base on really quick was AI. And Dave, I'm going to queue this one up for you really quick. We mentioned Microsoft a few times and this is what made me want to skip ahead a little bit to this question. Microsoft is investing heavily in AI, and when we talk about making sure the correct data is available to make the correct business decision when it’s needed, how do you see AI continuing and maybe improving on that process in the future?
Dave: Yeah, we're seeing it in a range of ways. We are gathering an incredible amount of data. We're using Power BI and those capabilities to analyze that and take that data and create analytical categories that we can act on. And that's enabled with some of the AI that they're exposing throughout their tool set. Power Automate, Power Apps, and Power BI are now all able to leverage different pieces of AI to help turn some of those things that used to require Masters-level data scientists, and let people who are not your “average bear” on your manufacturing floor.
People with relatively straightforward technical skills are able to turn that data into actionable data, and that's huge. We're seeing the vision go off and expose it and bring that forward, so people in quality are able to make judgments about machines they are nowhere near. By looking at imaging and saying “Wait a minute, that's fine, we can move ahead with that/no, we can't”. You know we're using AI to say it, but anything that isn't normal, we want to get in front of the people in quality so they can understand what the spec is. And instead of in the old days we defined imaging solutions that looked at good or bad or measurements and so that's what we need. Because it's measured properly, even if it's got a substantial blemish or cosmetic problem - It’s massively different now when we were talking about bringing forward anything that doesn't look the way it should and letting AI help make decisions about it in real time.
9. Data and access to data is changing the way we make business decisions. Has access to Data made a large impact on your manufacturing operations? How?
Andy: I think the keyword, at least to me, that you said there was actionable data that's really kind of the key there. Tod, I want to kind of run this one by you.
Tod: It is absolutely critical. My experience has been really when you start to see increased collaboration with data, increased factory efficiencies, using the data to understand better cost management, better employee experiences, and even to some extent the predictive maintenance that we talked about. Those are just a few examples of how critical it can be.
For instance, if a company has machines and processes that are connected to the cloud with all the predictive maintenance measures in place, and AI using and running in the background, they’re able to anticipate when those machines should be either upgraded or maintained in some shape or form. Those machines tend to not break down as often, and that alleviates a lot of the idle situations, whether it's employee or machines and not getting product out the door. So those situations are alleviated simply because of data and being able to make decisions based off of what AI is telling us.
You know, certainly data aggregation in the cloud is one of the most useful tools in manufacturing moving forward, and some of the key benefits are regional off premise monitoring, comparative data intelligence across global and regional factories, real time supply chain management oversight, greater asset tracking, and the predicted maintenance scheduling.
Andy: Pete, Dave. Any thoughts on top of that?
Pete: I’d just add that it's important to recognize the quality control, the QC, part of this discussion as well. And there's a lot of companies out there that fall short of quality control on some of the basics. The “basics” is what's the forecast for the demand plan in the proper granularity out over the horizon. You if you don't have that then you don't have the ability to act on that. Believe it or not, there's a lot of companies in the millions of dollars of revenue and even in the billions that still, in this day and age, have inventory accuracy problems. The floor inventory, whether it's a finished good or a raw material, doesn't reflect what the system’s saying.
How can that be? Well, process stuff, right? Process steps and then mapping mapping capacity to demand- all the data that's associated with a capacity statement. We talked before about master data and transaction data and whether you have latency or completeness issues.
Some of the basics that are driven well by good processes is a topic not to not to be forgotten here, because it sets up all of the innovation technology that we're talking about as well.
Andy: Gotcha, good insights, good insights.
10. From a Business Continuity Perspective, do you feel like most manufacturers are prepared to weather future disasters? Does new and emerging technology like Azure Site Recovery and Azure Backup change this in your opinion? Have we learned our lesson from COVID?
Andy: So we've been talking about data access to data. We're talking about AI. We've got all this technology we've been talking about, right? And, you know, there always comes a point where technology there's a problem or goes down or becomes unavailable. Technical problems, right? And what I'm thinking about that in the larger scope of what we're dealing with as a world right now? Covid, right?
It makes me think about business continuity. So what happens in the event of a disaster if we go back to March, April, right when COVID really hit in the lock down lock down started happening, everybody was freaking out, right? Everyone is like OK, what's happening? What's going to happen? Everybody tries to get their crystal ball out and figure out what's going to happen from a business continuity perspective.
And Pete, I'm going to pick on you first on this one: Do you feel like manufacturers are prepared to weather future issues like covid, do you think we've learned our lesson?
Pete: Well, certainly COVID makes collaboration more difficult. Not impossible, but more difficult. And if you break up a lot of what manufacturing folks and supply chain folks do - you could say there's the planning part of it, and then there's the execution part of it, right? And I think the planning part, given a COVID environment, is probably the easier of the two to affect going forward. You know you can do Zooms, you can have Webex meetings and so on and so forth. You can get the demand plan or the supply plan or a schedule, or a capacity plan out for everybody to see.
Where the collaboration challenge exists in a COVID sort of world is what are the learnings were bubbling up from the shop floor that can find their way into data or making a better plan the next time around. And some of that communication is easier to happen in the non-COVID environment; You walk down to the factory floor and you talk to Joe on line 2. It’s much easier in the non COVID environment. In the COVID environment, I think some of that execution and the learnings that go around that tend to fall short and I think that's the heartache, and I think that's probably where emphasis would be best placed.
Andy: Gotcha. Tod, Dave, any thoughts?
Tod: You know to add, Pete brings up some great comments relative to COVID versus non-COVID, and the reality is we didn't know about COVID before and we don't know what the next one is going to be. So the overall question of being prepared and weathering future disasters I can say that manufacturers and even ourselves have certainly gotten better because of COVID. We're better prepared because of what has happened. Are we 100% prepared moving forward? Probably not, but that's what I mean by the key that manufacturers, the more agile they are, the more they have the ability to be better the next time around when a future disaster does come upon us. we will be. And like I said, we're better than we were yesterday, but probably not as good as we need to be tomorrow.
11. Do you feel like the industry 4.0 movement is leading the charge in terms of modernizing technology for Manufacturers? Why?
Andy: Do you feel like the industry for data movement is really leading the charge in terms of modernizing technology for manufacturers and really sperring that digital transformation for manufacturing?
Pete: From what I hear in my client base is it's in the early stages of discussion with most of my clients. In many companies, it's not even in the conversation at all. They tend to dialogue in terms of we gotta get more efficient/I got too much inventory/I got too much downtime. You know, the traditional manufacturing sorts of sorts of metrics. So I haven't heard a lot of conversation of Industry 4.0 being the bundling term that moves executive managers and manufacturing forward.
I think that whole interconnectivity thing is on everybody's mind. But I don't think the nomenclature has gotten standardized from my perspective.
Andy: Tod, Dave, you guys seen anything different?
Dave: But well, I think I think you're right, Pete, there is some awareness level of “OK, we know there's this Industry 4.0 thing that's happening. We don't know where it's happening. We maybe haven’t adapted yet.” We're seeing some clients who are still struggling with those basic blocking and tackling types of things.
We are seeing folks who target improvements who go “I don't know. You can call that industry 4.0 or not, but I want to be able to do that.” Whether that is 100% inspection of my parts and I'm in a rapid, repetitive manufacturing environment and I just can't keep up, or I want to be able to see all my process parameters at once - I need to keep some of those for maybe food safety or to support the work I do in the process world, to the receivers of the process to my customers.
I don't know that they aren't all calling it Industry 4.0. They're seeing these things with big data with better analytics with IoT devices that can hook up to their old machinery and make it quote smarter or at least visible. They're plugging in the pieces of that they feel they need.
Tod: Yeah, just to add to that. Great comments, and what it boils down to is industry 4.0. - it's not a new term. It's been around for several years. It's really about kind of like that adoption rate though, right? When we think about how cloud infrastructure has changed over the course of the past three or four years, it's certainly gotten better. New and defined technologies and how we collect data in the rapid connectivity piece. Those technologies have gotten better, right? So in the past and growing the adoption rate into 4.0, are we there yet? Probably not yet. Do we see it changing in the future? Yeah, I mean it takes 8-10 years to move mountains, right? So definitely will see the adoption rates start to pick up. Definitely start to see how technologies are getting bigger and better and the demand for that right continues to push the boundaries and re-modernizing technologies.
12. Are cloud technologies like those in the Microsoft Azure and M365 platforms helping to achieve the goals and practices laid out by the Industry 4.0 movement?
Dave: I think it starts with the cloud that allows us to spin things up quick. We do trials or do proof of concepts. We make mistakes quickly, we learn from them quickly, we tear down the things we don't need and there's no ongoing costs. It's much more about iterating through to find the right combination of solutions than it is trying to say “I've perfectly planned it and I know what I'm going to get out of this data. I'm going to build the entire thing and it's going to be great.”
That takes a lot a lot of time. Instead we put some connectors into the cloud, get some data going, and start to analyze it. We can do things with web services that are very dynamic. We can use Power Automate and all those kinds of tools we can chain together data streams whether they be for alerting or for security, or for other kinds of solutions - For vision. For all of those, and we begin to iterate on them and get better and better and better. If we stop to get perfect, it never happens.
Andy: That's great advice. Tod. I saw you kind of nodding your head there. It looks like you've seen that one from experience.
Tod: Yeah, the data piece, right? I mean, data - the cloud, the aggregation of data, the data management, the data processing - all the critical pieces and elements to what the data is telling you. Is there a one solution fits all? Absolutely not. It's iterative. It's understanding. You know, getting data, managing it, understanding Power BI, understanding what the data is telling you, and then morphing. And that's where the agility comes in. It takes several iterations to get there. Just like Dave said.
Pete: And and just to piggy back a little bit, if you look at the portfolio of manufacturing automation that's around the piece, there's a lot of old equipment out there. And a lot of old equipment that doesn't talk to anybody or anything. So IoT comes to mind, and in many cases just the ability to understand is that machine on or off (and if it's on, how fast is it going) can provide massive value. So getting that information in real time to make decisions and also up in the cloud for analysis purposes has given a lot of those old equipment environments some pretty significant value. Whether you're going into hazardous environments or the decision maker has got some distance between him or herself and the and the floor, just that knowledge of what's happening on some of the basics is pretty valuable.
Dave: High visibility matters.
ABOUT INSITE BUSINESS SOLUTIONS:
InsITe helps businesses and manufacturing companies get the most out of current and emerging technologies with a customized IT approach to maximize growth, efficiency, insights, and productivity. InsITe is not a typical IT company selling products for short-term, short-sighted fixes. We invest in long-term solutions for a company’s growth by taking the time to learn its products, process, and business goals before bringing tech into the conversation. In this way, we become much like our Clients’ very own internal IT department with familiar faces who understand the business.
If you have any questions about this post please leave a comment. We read and respond to all comments. Or better yet, give us a call and ask to talk directly to our Founder and CEO Mike Schipper 616-383-9000.